The disadvantage of small cheap grinders is the lack of a smooth start and adjustment of revolutions. Everyone who included a powerful electrical appliance into the network, noticed how at this moment the brightness of the network illumination drops. This is due to the fact that at the time of launch powerful electrical appliances consume a huge current, respectively, the network voltage drops. The tool itself can fail, especially the Chinese with unreliable windings.
The soft start system will protect both the network and the tool. There will also be no strong kickback at the moment of switching on. And the speed controller will allow to work for a long time without overloading the tool.
The presented scheme is copied from an industrial design, installed on expensive devices. It can be used not only for the grinder, but also for the drill, milling machine, etc., where there is a collector engine. For asynchronous motors, the circuit will not work; a frequency converter is required there.
At first I drew a printed circuit board for the soft start system, without components for adjusting the speed. This is done on purpose, because In any case, the regulator must be wired. Having a scheme, everyone will figure out what to connect.
In the circuit, the regulating element is a dual operational amplifier LM358, through the VD1 transistor that controls the power triac BTA20-600. I did not get it in the store and put the BTA28 (more powerful). For a tool up to 1 kW, any triac with a voltage of more than 600V and a current of 10-12A will do. Because The circuit has a soft start, then the starting currents do not burn such a triac. During operation, the triac heats up and should be installed on the radiator.
The phenomenon of self-induction, which is observed when the circuit is opened with inductive load, is known. In our scheme, the circuit R1-C1 suppresses self-induction when the grinder is turned off and protects the triac from breakdown. R1 from 47 to 68 ohms, power 1-2W. 400V film capacitor.
Resistor R2 provides current limiting for the low-voltage part of the control circuit. This part itself is both a load, and to some extent, a stabilizing link. Due to this, after the resistor can not stabilize the power. Although there is a variant of the same scheme with an additional zener diode. I did not put it, because the supply voltage of the chip, so in the normal range.
Possible replacements of low-power transistors are listed under the circuit.
The adjustment of the regulator is done using the multiturn resistor R14, and the main adjustment by the resistor R5. The scheme does not give power adjustment from 0, but only from 30 to 100%. If you need a more simple powerful regulator from 0, then you can build a version proven over the years. It is true for the Bulgarian getting the minimum power is meaningless.
Due to the design features, the start of the angle grinder is associated with high dynamic loads. Due to the mass of the working disk, at the beginning of rotation, the inertia forces act on the gearbox axis. This entails some negative points:
- With a sharp start, the loads on the axle create an inertial jerk that, with a large diameter and mass of the disc, can pull the power tool out of the hands;
- With a sharp supply of operating voltage to the motor, an overcurrent occurs, which passes after a set of nominal speed;
- A large torque at a sharp set of revolutions prematurely wears gears of the gearbox of angle grinders;
- Overload, which perceives the working disk can destroy it when you start the engine.
IMPORTANT! When starting the grinder, always hold the tool with both hands, and be prepared to hold it. Otherwise you can get hurt. This warning is especially true for heavy diamond or steel discs.
As a result, the brushes wear out and both motor windings overheat. With constant switching on and off of the power tool, overheating can melt the insulation of the windings and lead to a short circuit, with subsequent costly repairs.
In some cases, it is possible to break off the teeth and jam the gearbox.
Therefore, the presence of a protective cover is required.
IMPORTANT! During the start of the grinder, the open sector of the casing should be directed away from the operator.
To better understand the mechanics of work, consider the device of the grinder in the drawing. All elements experiencing overload during a sharp start are clearly visible.
Schematic drawing of the location of the working bodies and control systems in the Bulgarian
To reduce the harmful effects of a sharp start, manufacturers produce grinders with adjustable revolutions and a smooth start.
Adjustment of turns is on the tool handle
But such a device is equipped only with models of the middle and high price category. Many home craftsmen acquire angle grinders without a regulator and slow down the starting speed. Especially it concerns powerful copies with a diameter of a cutting disk more than 200 mm. Not only is such a grinder hard to hold in the hands during start-up, the wear of the mechanics and the electrical part happens much faster.
Only one way out - to establish a smooth start grinders themselves. There are ready-made factory devices with speed control and slowing the start of the engine when starting.
Ready device to adjust the soft start
Such blocks are installed inside the case, in the presence of free space. However, most users of angle grinders prefer to make a circuit for the smooth start of the grinder independently, and connect it to the break of the power cable.
How to make a soft start scheme for an angle grinder with your own hands
The popular circuit is implemented on the basis of a control chip of phase regulation KR118PM1, and the power part is made on triacs. Such a device is simply mounted, does not require additional configuration after assembly, and therefore, a master without specialized education can make it, it is enough to be able to hold a soldering iron in his hands.
Electric soft start adjustment circuit for grinders
The proposed unit can be connected to any power tool, designed for alternating voltage of 220 volts. Separate removal of the power button is not required, the modified power tool is switched on with a regular key. The circuit can be installed both inside the case of the grinder and in the gap of the power cable in a separate case.
The most practical is to connect the soft start unit to the outlet from which the power tool is powered. The input (XP1 connector) is powered by 220 volts. To the output (connector XS1) connects the expendable outlet, which is plugged into the angle grinder.
When the start button of the grinder is closed, voltage is applied to the DA1 chip through the common power supply circuit. On the control capacitor is a smooth increase in voltage. As the charge, it reaches the working value. Due to this, the thyristors in the composition of the microcircuit do not open immediately, but with a delay, the time of which is determined by the charge of the capacitor. Triac VS1, controlled by thyristors, opens with the same pause.
Watch the video for a detailed explanation of how to make and what scheme to apply
In each half-cycle of alternating voltage, the delay decreases in an arithmetic progression, as a result of which the voltage at the input to the power tool gradually increases. This effect determines the smooth start of the engine of the Bulgarian. Consequently, the disk revolutions increase gradually, and the gearbox shaft does not experience inertial shock.
The time of the set of revolutions up to the working value is determined by the capacity of the capacitor C2. The value of 47 microfarads provides a smooth start for 2 seconds. With such a delay, there is no particular discomfort to start working with the tool, and at the same time the power tool itself is not subjected to excessive loads from an abrupt start.
After turning off the angle grinder, the capacitor C2 is discharged by the resistor R1. With a rating of 68 kΩ, the discharge time is 3 seconds. After that, the soft starter is ready for a new start-up cycle of the grinder.
With a slight revision, the scheme can be upgraded to the engine speed regulator. For this resistor R1 is replaced by a variable. Adjusting the resistance, we control the engine power, changing its speed.
Thus, in one case you can perform the engine speed control and soft starter power tools.
The remaining details of the scheme work as follows:
- Resistor R2 controls the amount of current flowing through the control input of the triac VS1;
- Capacitors C1 and C2 are components of the control chip KR118PM1 used in a typical wiring diagram.
For simplicity and compactness of installation, resistors and capacitors are soldered directly to the legs of the microcircuit.
Triac VS1 can be any, with the following characteristics: maximum voltage up to 400 volts, minimum throughput current 25 amperes. The magnitude of the current depends on the power of the angle grinder.
Due to the smooth start of the grinder, the current will not exceed the rated operating value for the selected power tool. For emergency cases, for example, jamming of the LBD disk - a current margin is required. Therefore, the nominal value in amperes should be doubled.
The nominal values of the radio components used in the proposed electrical circuit are tested on a two kW kW angle grinder. Power reserve is up to 5 kW, this is due to the peculiarity of the KR118PM1 chip.
The scheme is working, repeatedly executed by home craftsmen.
If you have an old angle grinder in your arsenal, do not rush to write it off. Using a simple electrical circuit, the device can be easily upgraded by adding to it the function of changing the frequency of revolutions. Thanks to a simple regulator, which can really be assembled with your own hands in a few hours, the functionality of the device will increase significantly. Reducing the rotational speed, the grinder can be used as a grinding and sharpening machine for various types of materials. There are new opportunities for the use of additional attachments and accessories.
For what Bulgarian low speed?
The built-in drive speed control feature allows you to delicately handle materials such as plastic or wood. At low revs increases comfort and safety. This function is especially useful in electrical and radio installation practice, in car-care centers and restoration workshops.
In addition, among professional users of power tools there is a strong opinion that the simpler the machine is, the more reliable it is. And additional service "stuffing" is better to bring out of the power unit. In this scenario, the repair of equipment is greatly simplified. Therefore, some companies specifically produce remote individual electronic regulators that are connected to the power cord of the machine.
Speed controller and soft start - for what you need
In modern Bulgarians use two important functions that increase the reliability and safety of the instrument:
- speed control - a device designed to change the number of revolutions of the engine in different modes of operation;
- soft start - a scheme that provides a slow increase in engine speed from zero to maximum when the device is turned on.
Used in electromechanical tools, the design of which uses a collector engine. Help reduce the wear of the mechanical part of the unit during start-up. Reduce the load on the electrical elements of the mechanism, launching them into work gradually.
Studies of the properties of materials have shown that the most intensive development of friction nodes occurs during an abrupt transition from a state of rest to a fast motion mode. For example, one start of an internal combustion engine in a car is equal in terms of wear of the piston group to 700 km of run.
When the power is turned on, an abrupt transition occurs from a state of rest to a disk rotation at a speed of 2.5–10 thousand revolutions per minute. Those who worked with the grinder are well aware of the feeling that the machine is simply “breaking free”. It is at this moment that the overwhelming amount of breakdowns associated with the mechanical part of the unit occurs.
The stator and rotor windings are also under stress. The collector engine starts in short circuit mode, the electromotive force is already pushing the shaft forward, but inertia still does not allow it to rotate. There is a jump start current in the coils of the electric motor. And although they are constructively designed for such work, sooner or later there comes a moment (for example, during a voltage surge in the network) when the winding insulation does not withstand and interturn closure occurs.
When the soft start and the engine speed changes are included in the electrical circuit of the tool, all the problems described above automatically disappear. Among other things, the problem of “failure” of the voltage in the general network at the time of launching a hand tool is solved. This means that the refrigerator, television or computer will not be exposed to the danger of "burnout". And the automatic circuit breakers on the meter will not work and turn off the current in the house or apartment.
The soft start scheme is used in medium and high price grinders, the speed adjustment block is mainly used in professional angle grinders.
Adjustment of turns allows the grinder to process soft materials, to perform fine grinding and polishing - at high speed the wood or paint will simply burn.
Additional wiring diagrams increase the cost of the tool, but increase the service life and safety level at work.
How to assemble a regulator circuit with your own hands
The simplest power regulator, suitable for grinders, soldering irons or light bulbs, is easy to assemble with your own hands.
Circuit diagram
In order to assemble the simplest speed control for the grinder, it is necessary to purchase the parts shown in this diagram.
Schematic diagram of the speed controller
- R1 - resistor, resistance 4.7 kΩ;
- VR1 - trimmer, 500 kΩ;
- C1 is a 0.1 μF x 400 V capacitor;
- DIAC - triac (symmetrical thyristor) DB3;
- TRIAC - Triac BT-136/138.
Work scheme
The VR1 trimming resistor changes the charge time of capacitor C1. When voltage is applied to the circuit, at the first moment of time (the first half period of the input sinusoid), the triacs DB3 and TRIAC are closed. The output voltage is zero. Capacitor C1 is charging, the voltage on it increases. At a certain point in time, set by the chain R1-VR1, the voltage on the capacitor exceeds the opening threshold of the triac DB3, the triac opens. The voltage from the capacitor is transmitted to the control electrode of the TRIAC triac, which also opens. Through the open triac current begins to flow. At the beginning of the second half cycle of the sinusoid, the triacs are closed until the capacitor C1 is recharged in the opposite direction. Thus, the output is a pulsed signal of complex shape, the amplitude of which depends on the operating time of the circuit C1-VR1-R1.
Assembly procedure
Assembly of this scheme does not complicate even a beginner radio amateur. Parts are available, you can buy them in any store. Including vypayat from old boards. The order of assembly of the regulator on thyristors is as follows:
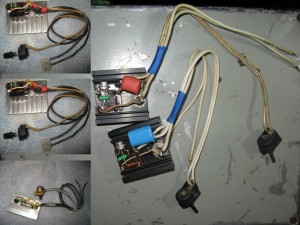
How to connect the device to the grinder, options
The connection of the regulator depends on what type of instrument is selected. If a simple circuit is used, it is enough to mount it into the power supply channel of the power tool.
Installing a homemade board
There are no ready-made installation recipes. Everyone who has decided to equip the angle grinder with a regulator has it in accordance with its goals and instrument model. Someone inserts the device into the holder's handle, someone into a special additional box on the case.
In different models, the space inside the housing of the grinder may be different. Some have enough free space to install the control unit. In others it is necessary to carry it to the surface and fix it in another way. But the trick is that, as a rule, a certain cavity always exists in the back of the instrument. It is designed for air circulation and cooling.
Cavity in the back of the apparatus
Usually it is here that the factory speed regulator is located. A handmade scheme can be placed in this space. So that the regulator does not burn out, thyristors should be installed on the radiator.
Video: soft start plus and engine speed adjustment
Features of the installation of the finished unit
When buying and installing a factory regulator inside the grinder, most often you have to modify the case - cut a hole in it to bring the adjusting wheel. But this may adversely affect the rigidity of the casing. Therefore, it is preferable to install the device outside.
The adjusting wheel changes speed
The numbers on the adjusting wheel indicate the number of revolutions of the spindle. The value is not absolute, but conditional. "1" - the minimum speed, "9" - the maximum. The remaining figures are used for orientation in the regulation. The location of the wheel on the body is different. For example, on the Bosch PWS 1300–125 CE, Wortex AG 1213–1 E or Watt WWS-900, it is located at the base of the handle. In other models, such as the Makita 9565 CVL, the adjustment wheel is located at the end of the casing.
The connection diagram of the regulator to the grinder is not difficult, but sometimes it is not so easy to stretch the cables to the button, which is located on the other end of the device. The problem can be solved by selecting the optimal cross-section of the wire or bringing it to the surface of the casing.
The regulator is connected according to the scheme
A good option is to install a regulator on the surface of the device or to attach it to a network cable. Not always everything turns out from the first attempt, sometimes the device has to be tested, after which it is necessary to make some corrections. And this is easier to do when access to its elements is open.
Important! If there is no experience with electrical circuits, it is more expedient to purchase a ready-made factory regulator or LBM equipped with this function.
Attachment to the power cord
Manual device
The main rule in the operation of the Bulgarian with a homemade speed control - compliance with the mode of work and rest. The fact is that an engine operating at a “regulated” voltage is particularly hot. When grinding at low revs, it is important to take frequent breaks so that the collector windings do not burn out.
It is also extremely not recommended to turn on the tool, if the speed regulator is set to minimum - the undervoltage is not enough to rotate the rotor, the collector lamellae will remain in short circuit mode, the windings will start to overheat. Unscrew the variable resistor to the maximum, then turning on the angle grinder, reduce the speed to the desired value.
Observance of the correct order of inclusion and adjustment will allow to operate the Bulgarian indefinitely for a long time.
In addition, it should be understood that the speed adjustment on the grinder is based on the principle of a water tap. The device does not increase the number of revolutions, it can only lower them. It follows from this that if the maximum passport speed is 3000 rpm, then when the speed controller is connected, the Bulgarian will work in the range lower than the maximum speed.
Attention! If the angle grinder already contains electronic circuits, for example, it is already equipped with a speed controller, then the thyristor controller will not work. The internal circuits of the device simply will not turn on.
Video: self-made regulator of turns of LBM
Equipping the grinder with an engine speed control circuit will increase the efficiency of using the device. and expand its functional range. It will also save the technological resource of the grinding machine and increase its service life.
The grinder, or grinder, is often necessary on the farm for metalworking. In addition, it can be used to clean both wood and stone materials. It is difficult to imagine the implementation of industrial work without grinders. This is a tool that will suit both a professional in his work and an amateur in household chores.
Bulgarian with adjustment of turns and smooth start
When working with your hands, it is important that the power tool was a smooth start. This is especially true if you often have to work, and the network does not withstand the voltage of the tool.
The budget options for angle grinders - angle grinders - have several disadvantages:
- The power tool does not have the ability to smooth, soft start. This can lead to power outages, as the Bulgarian in the first seconds after switching on consumes a large amount of electricity. There is also a huge possibility of damage to the motor and tool breakage after being carried out not with a soft start, but abrupt, with jerks.
- The power tools, especially simple Chinese ones, do not have a speed controller (speed adjustment can ensure long tool operation without a load on it).
Therefore, when choosing a tool, it is very important to pay attention to such parameters as speed adjustment and the presence of a soft start. In addition, when choosing the angle grinder should pay attention to power. Here the main indicator is the volume of work performed.
If the work is not large-scale and not frequent at the household level, then fit a power tool with an adjustment of 125 mm and a power between 600-900 watts.
For large-scale work on an industrial scale, use angle grinders more than twice as powerful. More to the main indicators in addition to technical characteristics, is safety. The grinder should be safe. What does it mean? First, as already mentioned, the presence of a soft start, which prevents power surges during switching on. Automatic fuses, necessary for the emergency stop of the motor during a system failure. Fuses serve as a regulator when the circle is wedge. Dust protection is provided. It is necessary with frequent use of the grinder so that the dust does not accumulate in the tool.
The function of the heat sink is important. Heat sink protects against overheating. During operation, especially if the work is continuous, the machine body is subject to strong heating, so that there is no overheating and heat removal is necessary. When overloaded, the angle grinder stops - this happens during heating, approaching 200 o C. Well, the disk balancing serves to reduce unpleasant vibration and instrument beating during operation, especially old worn discs are affected. It is very important to pay attention to and pay attention to safety when choosing a tool and further working with it.
When choosing a tool it is worth noting that there are grinders with one and two handles. Here one should rely solely on convenience. Two-handed models are likely to be more comfortable to hold, but such tools are heavier in weight, one-handed models will also have to be held with two hands, but such angle grinders are smaller in size and weight.
The leaders in the power tool market are Bosch. Tools of this company have all the necessary characteristics from convenience to security. Also, the advantages of Bosch tools are that there is good ventilation.
BT136 600E: Voltage Adjustment Switch On Circuit
Cheap Bulgarians that do not have enough power, manufacturers do not burden the inclusion of voltage regulation, otherwise such grinders would already not be cheap. When starting the grinder, if it is smooth, the process is carried out through an adapter connected by contacts with a rectifier unit. Rectifier unit converts current.
But sometimes it makes sense to modernize the Bulgarian using the established scheme. Circuit is assembled quite simply. It is not difficult to make it, and if you wish, you can connect not only the grinder, but any other tool to the finished circuit. However, the instrument must have a collector motor, not an asynchronous one.
The self-made approach to creating the scheme will be as follows.:
- To get started, download the board if it is not there;
- The simulator Bt136 600E is used as a power link;
- During operation, the triac will heat up to avoid this; a heat sink is installed;
- The resistors used give resistance to current, providing current absorption;
- Adjustment of the regulator occurs due to the multiturn trimming resistor;
- To check, you must connect a light bulb;
- After connecting the light bulb must be turned off - the triac must be cold;
- Connecting the resulting circuit to the grinder.
If the board is properly connected, the triac and the angle grinders should start up smoothly, and the use of the speed should be adjustable. After that, you can test the grinder in the case. Such knowledge may be needed in the repair of motor faults. For example, when the voltage rises or there is an incorrect balancing.
The regulator of turns for the Bulgarian with the hands
When using ingenuity to create a regulator of turns with your own hands, you can use the evaporated boards of the regulator of a sewing machine or vacuum cleaner. In addition, the components for the regulator are inexpensive and can be easily purchased if possible. It is worth noting that in the device the gearbox is needed to support a certain number of revolutions and speed. If the speed is increased, the reason is most likely in the stator. The stator needs repair. Stator repair is possible at home.
The work of the collector motor is provided by any kind of electrical voltage. When changing the power voltage, you need to reduce or increase the number of revolutions. Changing this number helps just the same thyristor speed controller.
Regulator Assembly Stages:
- First you need to unscrew the handle of the grinder, evaluate the place and figure out where to place the circuit elements (if there is no space, you can make the device in a separate box);
- The resistor can be made of aluminum;
- Under the condition of a slight heating of the triac, the radiator is sufficiently small;
- Next is the soldering of the structure.
In conclusion, there is a sizing of epoxy resin for fixing. Self-made device can work for years. There are cases when the device accelerates at high speeds after switching on - this means that the stator winding has closed. In this case, a coil closure occurred. The stator requires repair, most often it needs rewinding.
There are some typical faults: the winding is broken or burned, a short circuit occurs, an insulating surface breaks through.
We make the speed control
Electric grinder is impossible without a speed regulator, so that there is an opportunity to reduce the number of revolutions.
The regulator's scheme from the point of view of physics looks like:
- Resistor - R1;
- Trimmer Resistor - VR1;
- Capacitor - C10;
- Triac - DIAC;
- Triac - TRIAC.
Electronic controller is not only built-in, but also external for convenience. In the Bulgarian company Bosch electronics sets the number of revolutions from almost 3 thousand to 11.5 thousand. There is no load on the power meter, all indicators are taken into account. Reducing the number of revolutions and increase them does not complicate the tool. Adjustable speed is simply necessary for any work grinder.
Making a smooth start for your own power tools (video)
Only at first glance, it seems that the Bulgarian may never be needed in life, that there will be no situations where it will be useful and even more so when it will have to be repaired. Of course, you can turn to professionals, and you can determine the problem yourself and try to fix it.
Attention, only TODAY!
Smooth start for grinders do it yourself
Cheap grinder is easy enough to upgrade to significantly increase its service life so that it does not jam the gearbox and does not blow the winding armature wires. Usually these problems are peculiar to a sharp start of an inexpensive grinder.
All modernization consists only in the assembly of a simple circuit in an external box.
The prototype design in the figure below was used to adjust the heat of the lamps, that is, to work on a purely resistive load.
The basis of the design is the chip K1182PM1R. It is highly specialized, and as it does not sound strange today, domestic production. If necessary, the start time can be increased by putting a large capacitance of the capacitor C3. While this capacitor is charging, the electric motor gradually increases the speed to the maximum. A 68 kΩ resistor is optimally selected for our circuit. If you want to make a power regulator, then you need to replace the resistance R1 variables. Resistance is 100 kΩ and more.
In the role of an excellent enclosure of insulating material, a typical junction box will do. The socket is screwed to it and a cable with a plug is connected, which makes this design very similar to a self-made extension cord.
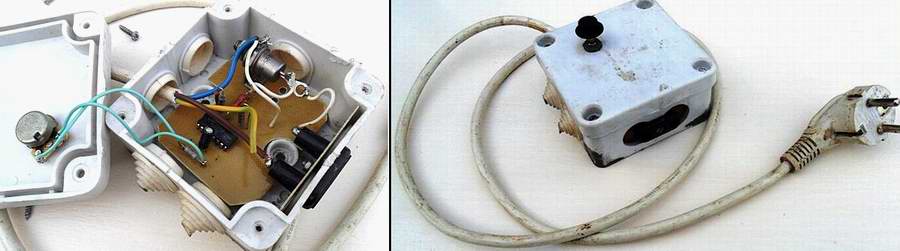
If you want, you can put together a slightly more complicated soft start scheme. It is typical for the XS – 12 module. It is installed in the power tool in the factory production of many firms.
If you want to regulate the speed of the connected electric motor, then the design becomes a bit more complicated: because the trimming resistor is set to 100 kΩ and the adjusting resistance to 50 kΩ.
In order to save, you can equip with a speed regulator typical grinder. Such a regulator for grinding housings of various electronic equipment is an indispensable tool in the amateur radio arsenal.